Cladding and insulation replacement on multi-storey flats
Benefits of collaboration between client, contractor and consultants.
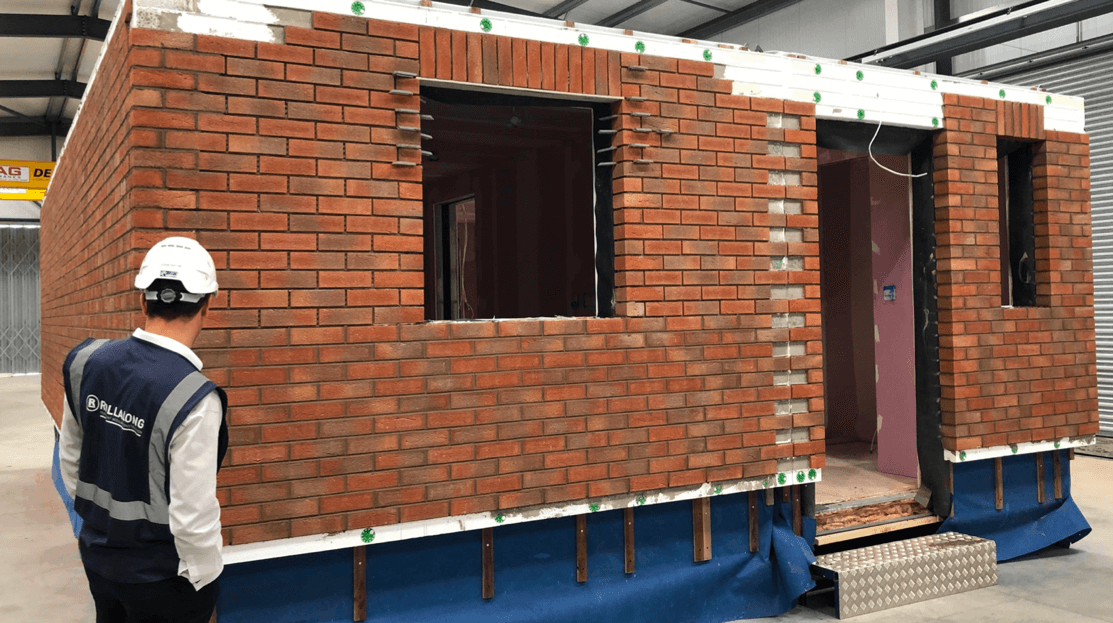
In March 2018 Kier Housing Maintenance was contracted by the Hyde Group to remove and replace external cladding and insulation at its 9-storey, mixed tenure Bolanachi Building, Bermondsey while it was fully occupied. It was a constrained site with minimum storage space and flanked by busy roads and a railway line serving central London.
Project requirements:
- Cladding and insulation to be removed, back to the final 12.5mm skin of plasterboard separating the homes from the work being undertaken.
- Work to be completed without disturbing or disrupting residents’ internal services and finishes.
- Building to be left in a watertight and secure condition at the end of every working day, with the new cladding panels fitted by the end of each week.
- Work to be completed in four phases to minimise disruption to residents and the local community, with a phased scaffold to the elevations.
Initial approach:
Before work started a full pre-condition survey carried out of the properties to determine existing damage and locate and identify any fittings, electrical or plumbing services located on or within the affected walls. Operatives were given this information on a daily basis during morning briefings, so they were fully aware of site conditions.
Problems and solution:
When the first panels were removed, Kier found complications with the underlying substructure. This required the works to be reprogrammed to remove and re-fix panels and insulation in quick succession, rather than the original requirement of a phased scaffold to the elevations. Collaboration with consultants Martin Arnold Associates identified a Gridline System as an appropriate solution to record and remedy defects (see Appendix).
A 5-day removal and replacement sequence devised.
Day 1: Existing cladding and other elements stripped back to the Steel Frame Structure (SFS). Existing SFS reviewed to agree any remedial work with client for completion on same day. Insulation installed between metal stud, followed by installation of cement board and waterproof layer.
Day 2: Secondary insulation installed, followed by installation of horizontal brackets.
Day 3: Fire breaks installed at floor level, party walls and around windows.
Day 4: Installation of fire breaks completed and rainscreen insulation installed. Vertical brackets started ready to receive new rainscreen cladding.
Day 5: Installation of vertical fire brackets completed and rainscreen cladding installed.
To assist any future contractor working on the site, the waterproofing layer was marked up with services information.
Conclusions and lessons:
- The Gridline System provided an effective and flexible solution to deal with unforeseen structural problems as existing cladding and insulation removed.
- Collaboration between client, contractor and consultants benefited all stakeholders, with operatives and residents having clear communication and knowledge of what was happening on site. The client achieved all its project requirements to schedule.
- Not only is the Gridline System a safe way of working but its repetitive nature created economies and efficiencies for all involved.
Appendix: Benefits of Gridline System
- Allowed Kier to better capture repetitive defects and clearly identify their location.
- Provided more assurance for Hyde, with better accountability, and full documentation and control – essential on a site where all materials were recorded at varying stages of their installation.
- Allowed locations of work to be clearly identified in weekly site reports.
- Enabled any remedial works emerging during the project to be clearly and easily recorded and managed.